For years, hazard communication (HazCom) compliance meant flipping through binders, using handwritten labels, updating spreadsheets, and chasing down safety data sheets over email. It was time-consuming, inconsistent, and often unreliable. As chemical usage grows and regulations evolve, these outdated methods no longer support the level of accuracy and accessibility required.
Mistakes in SDS management aren’t just inconvenient. They can jeopardize employee safety and trigger serious compliance violations. Fortunately, new technology has stepped in to help. Today’s SDS technology offers smarter, faster ways for EH&S professionals to organize, update, and access safety data, giving them the tools they need to manage compliance with confidence.
Why HazCom Is More Complex (and More Critical) Than Ever
The foundation of hazard communication is still OSHA’s Hazard Communication Standard (HCS), but the expectations surrounding it have grown significantly. Today, it includes the adoption of the Globally Harmonized System (GHS), expanded labeling requirements, and greater scrutiny around chemical classification. Meanwhile, the types and amount of chemical substances used in daily operations are increasing. From lithium-ion batteries in storage areas to specialized compounds on production lines, the potential risks are higher—and so are the consequences of getting things wrong.
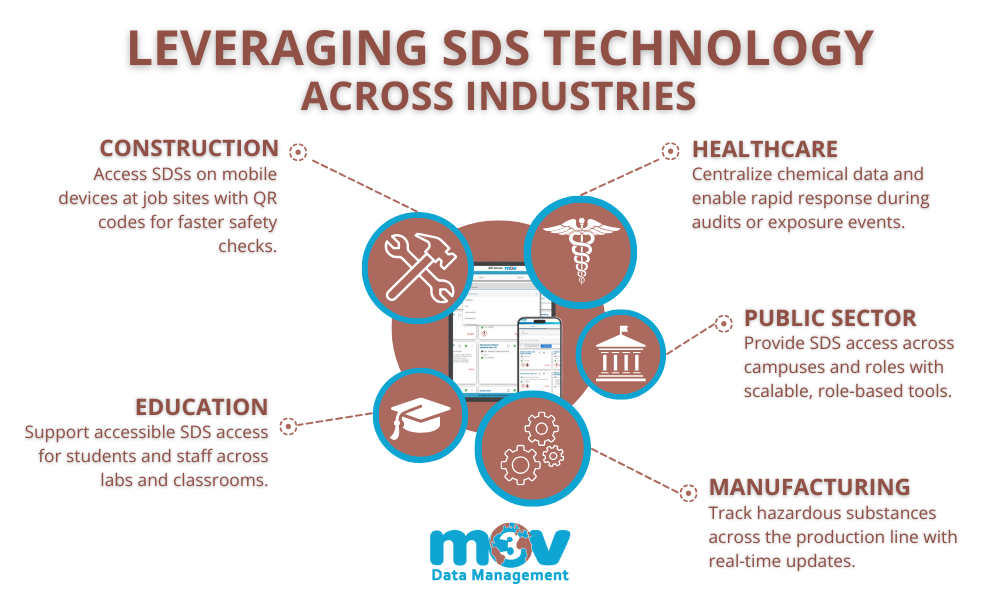
Industry Challenges
Industries like construction, healthcare, education, and manufacturing each face their own challenges. Whether it’s ensuring SDS access in a K–12 school lab or managing hazardous materials across a large-scale manufacturing facility, documentation and hazard tracking demand time, attention, and resources. EH&S teams are often managing more chemicals with fewer people, and trying to keep up using manual processes.
Spreadsheets and filing cabinets can’t keep pace with Tier II reporting, ongoing SDS updates, and new regulatory requirements. Technology is becoming essential for staying compliant and protecting the people behind the data.
SDS Technology: What It Is and Why It Matters
SDS technology takes the guesswork and legwork out of managing chemical safety data. Instead of relying on static files and outdated folders, EH&S teams can access live, web-based systems that update in real time. A modern SDS solution creates a centralized, digital library that pulls together SDSs from multiple vendors and storage locations into a single, searchable platform.
Key features include QR code access, GHS-compliant label creation, and automated update notifications. That means field crews can scan a code with a mobile device and pull up a safety data sheet in seconds, even from their phone. It also means fewer gaps in documentation, faster retrieval during audits or emergencies, and less time spent manually tracking chemical information.
Built for Real-World Compliance Needs
The right SDS platform supports alternate format text and multiple file types, helping organizations meet accessibility goals and accommodate assistive technology. For EH&S professionals, this isn’t just about ease. It’s about gaining reliable control over complex compliance tasks. From chemical tracking to label generation, SDS technology lays the foundation for safer, more efficient HazCom programs. It also provides an opportunity to apply technological expertise where it matters most—protecting people and streamlining processes.
Supporting Every User: How HazCom Tech Builds a Safer Workplace
HazCom isn’t just about meeting regulatory deadlines. It’s about making sure everyone can understand and access the information they need to stay safe. In many organizations, safety responsibilities are shared across teams, departments, and even buildings. That makes communication just as important as compliance. Modern SDS platforms are built with this in mind, offering tools that go beyond storage and searchability to support a more inclusive and accessible workplace.
Today’s systems are accessible in many formats and are compatible across multiple devices, making it easier for organizations to meet accessibility standards. This is especially important in schools, public institutions, and workplaces where student disability services or employee accommodations are part of daily operations. Features designed with assistive technology in mind help ensure that critical chemical safety data is available to all users, regardless of ability or role.
Remote access is a major advantage. Workers who are off-site, on alternate schedules, or navigating specific accessibility needs can still pull up SDSs on demand. With smart building systems and embedded platforms, organizations can manage SDS access by user, role, or location, offering the right data at the right time without compromising safety or control.
Tech That Works for You: What Smart HazCom Looks Like
The value of SDS technology is in the day-to-day work of your team. When a system is built with the user in mind, it helps people do their jobs more effectively. Field crews can scan a QR code and access the exact SDS they need in seconds, cutting down on response time during incidents or inspections.
Safety officers can cross-reference chemical substances with regulatory data instantly, using built-in tools that eliminate the need for juggling spreadsheets or checking multiple sources. Compliance tasks are easier to track and complete, thanks to email reminders and centralized dashboards. These tools make sure deadlines aren’t missed, forms aren’t overlooked, and audits are less stressful.
With a smart SDS system, professionals don’t have to guess where documents are, worry about version control, or spend hours manually updating files. Instead, they get clear visibility across every site, every user, and every task. That’s what practical, purpose-built innovation looks like. It gives teams the confidence to stay compliant and the flexibility to adapt when things change.
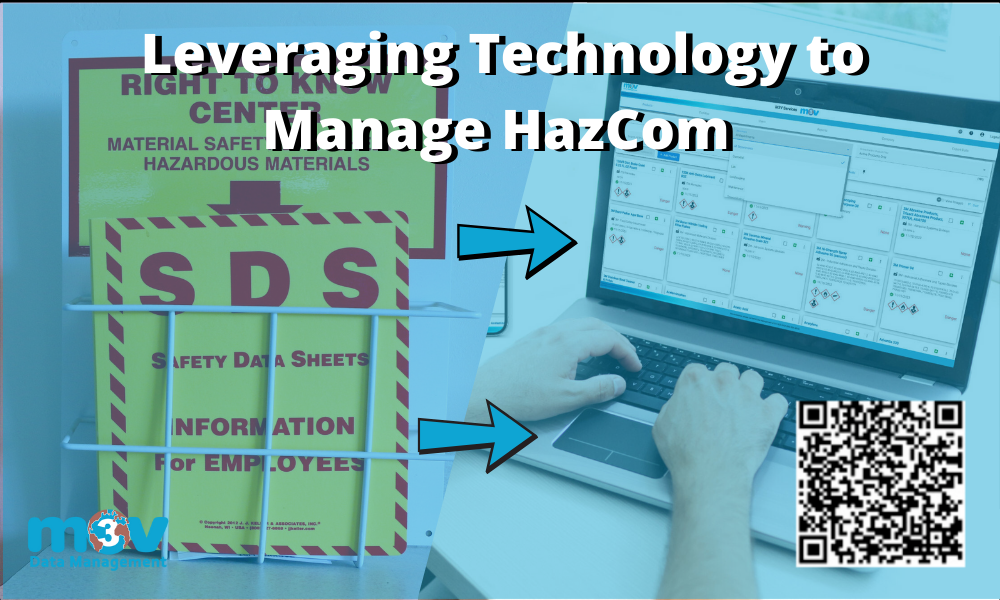
Here’s What to Look for in an SDS Solution
Not all SDS software is created equal. The right solution should make your job easier. Start by looking for a platform that’s fully compliant with the latest GHS standards and built to scale. Whether you’re managing SDSs for one facility or dozens, your system should be able to grow with your needs without sacrificing performance.
Ease of use matters just as much. An intuitive interface reduces training time and helps everyone find what they need without frustration. Responsive support is also key. Choose a provider with a track record of working alongside EH&S professionals, not just software developers.
Consider how the software fits your environment. Does it support multiple file types and alternate formats? Does it work seamlessly with your other systems in place? Is it adaptable for your specific use case, whether that’s a school district, a manufacturing plant, or an office building? Look for features like integrated label printing and QR code posters that allow employees to quickly access SDSs on the floor or in the field.
Also, think about who owns your data. A trustworthy platform will let you export your entire SDS library at any time, because your data should always stay in your hands.
Finally, consider how the software will evolve with your organization. The ideal solution should help you improve workflows, reduce risk, and maintain compliance without extra overhead. A platform that supports growth, accessibility, and reliable applications across multiple locations quickly becomes a trusted resource.
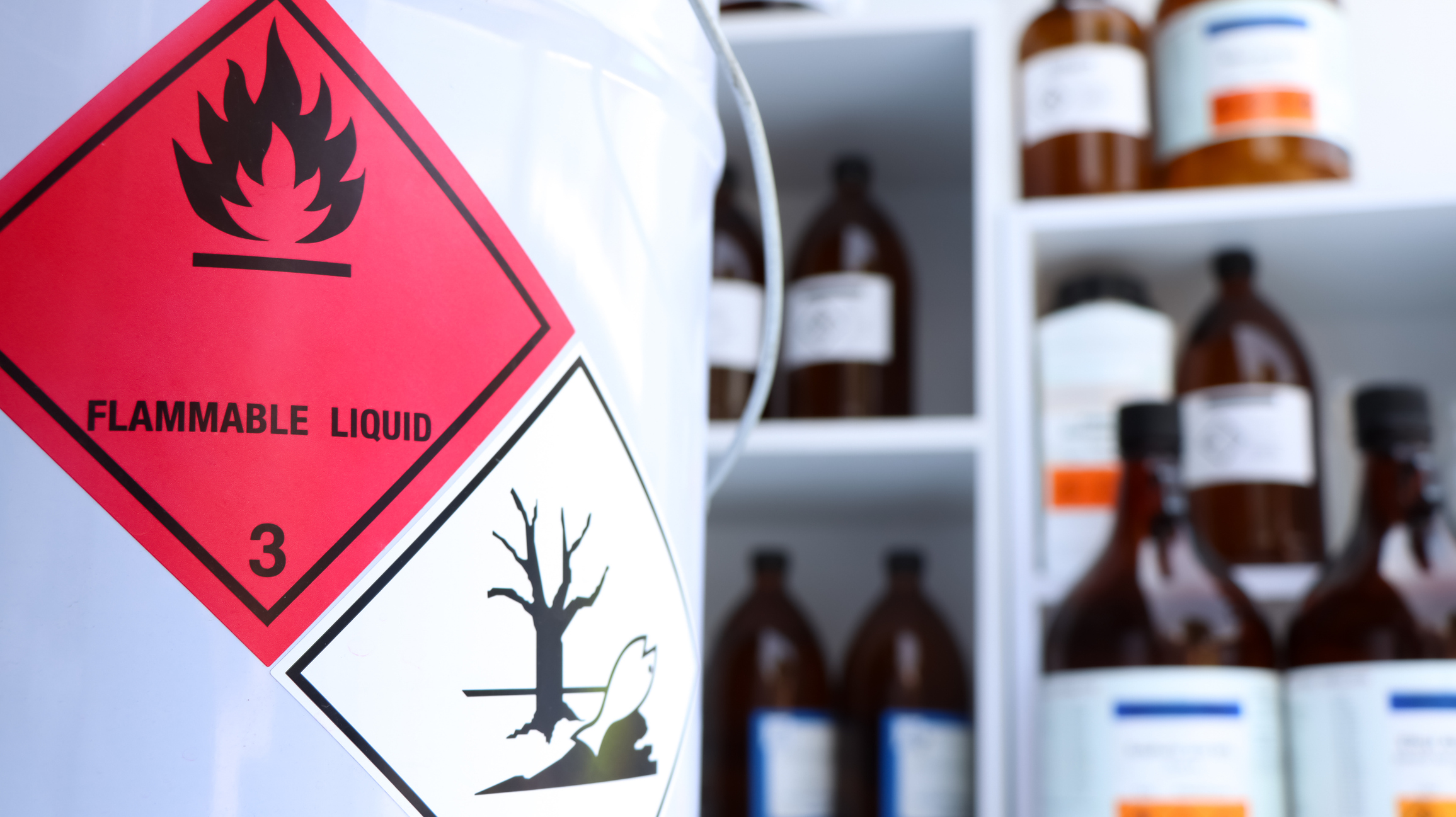
Smarter HazCom Starts with the Right Technology Partner
Staying compliant with hazard communication standards doesn’t have to mean more spreadsheets, more paperwork, or more stress. With the right SDS technology in place, EH&S professionals gain reliable access to the information they need. That kind of clarity improves decision-making, supports safety goals, and frees up time to focus on bigger priorities.
At M3V Data Management, we understand the challenges of managing chemical data because we’ve lived them. Our software was built by compliance professionals for compliance professionals, combining real-world insight with intuitive design. Whether you need to simplify your SDS library, improve your tracking process, or bring accessibility to the forefront of your HazCom program, our tools are designed to help you do more with less.
Our clients trust us to provide tools that work as expected, adapt to their environment, and support their teams with responsive support and prompt service when it matters most. Better access leads to better outcomes. If you’re ready to move beyond binders and start building a smarter HazCom system, contact M3V today.